By Jacob Lublin & Omri Hemo, R&D Engineers at Polyram
Electric and autonomous vehicles figured prominently at this year’s Plastic In Automotive Engineering (PIAE) Congress, with the transition to electric vehicles forecast to take place in the near future. This development raises a number of challenges for plastic automotive parts. Cooling systems will be based less on water and oil cooling and more on efficient dissipation of heat from the plastic parts themselves. This demands significantly enhancing the heat conduction of the polymer compounds while conserving their mechanical properties.
Summary
Polyram’s engineers report on the latest trends in the automotive industry as reflected in the recent PIAE congress and exhibition held in March of this year: electric and autonomous vehicles, focus on surface textures, plastics for the outer chassis, and a continuation of efforts to reduce weight.
Polyram and PIAE
Polyram consistently strives to develop tailor-made and innovative solutions that reflect shifting trends in the market. The company is focused on a number of industries, with the automotive industry prominent. Polyram ensures that all processes and products meet the most stringent regulatory requirements and is certified compliant to IATF 16949:2016.
In order to keep abreast of new developments and trends in the automotive industry, Polyram participates every year in the PIAE congress held in March in Manheim, Germany. Polyram also uses the accompanying exhibition to present its products. The congress focuses on new developments in plastics and plastic parts designed for automotive applications, giving participants an overview of innovations in materials and design that forecast how the industry is developing and changing. In the conference program presentations are given by automobile and parts manufacturers and manufacturers of plastic raw materials, while outside the lecture halls booths are set up where the manufacturers can display their products. Participation in PIAE is another resource helping Polyram to keep abreast of present customer needs and to develop research projects addressing the needs of the future.
The Future in Electric and Autonomous Vehicles
Electric and autonomous vehicles figured prominently at this year’s PIAE conference, with the transition to electric vehicles forecast to take place in the near future, to be followed by the next breakthrough, the large-scale introduction of autonomous vehicles. Electric vehicle design raises a number of challenges for plastics in automotive applications. Most significant is the difference in the engine environment between standard gasoline engines and electric motors. Cooling systems in electric vehicles will rely less on water and oil circulation and more on efficient heat dissipation from the plastic parts themselves. This will require the development of new plastic compounds based on use of additives for improved heat conduction that at the same time retain the required mechanical properties. Polyram is conducting extensive research to identify effective solutions to this challenge.
Another significant difference in electric vehicles is the increased risk of fire due to short circuiting. To address this, a further development program underway is new PP-long fiber compounds with improved flame retardancy. There is a technological challenge in combining a high loading of flame retardants in long-fiber-loaded PP, as the flame retardants tend to degrade when exposed to the high processing temperatures required for the fiber-PP compounds. Polyram has formulated a number of compounds to resolve this issue which are presently undergoing validation testing.
Another consequence of the perceived trend to electric vehicles can be seen lately in the production schedules of the big automobile makers. These are slowing production to avoid overstocking of conventional vehicles that may be hard to sell as electrics gain in popularity. This downturn is temporary, and production is expected to return to normal levels as market trends come into focus.

New Surface Textures
Another notable trend seen at the exhibition is the search for new surface textures, tactile sensations and innovative geometrical patterns for various parts and surfaces in the passenger compartment. These new features require new part design as well as new material properties to support the desired passenger experience. An outstanding example of this trend from the last exhibition is Ford’s new Fiesta model incorporating new types of surface texturing (Fig. 2). The main challenge in designing compounds for new textural surface effects is choosing the right materials (usually a combination of different polymers) and choosing the most suitable processing technology for achieving optimal surface effects in a cost-effective way.
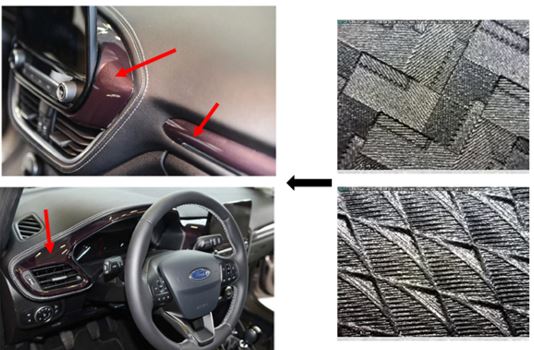
New Product – ABS Containing Long Glass Fibers – ABS LGF
The compounder Trinseo displayed a class of compound new to the market, ABS containing long glass fibers (ABS LGF). The compound is already in commercial use, replacing magnesium for display panels in some BMW models (Fig. 3). ABS LGF shows outstanding dimensional stability in comparison to long-fiber-filled PP and polyamide.
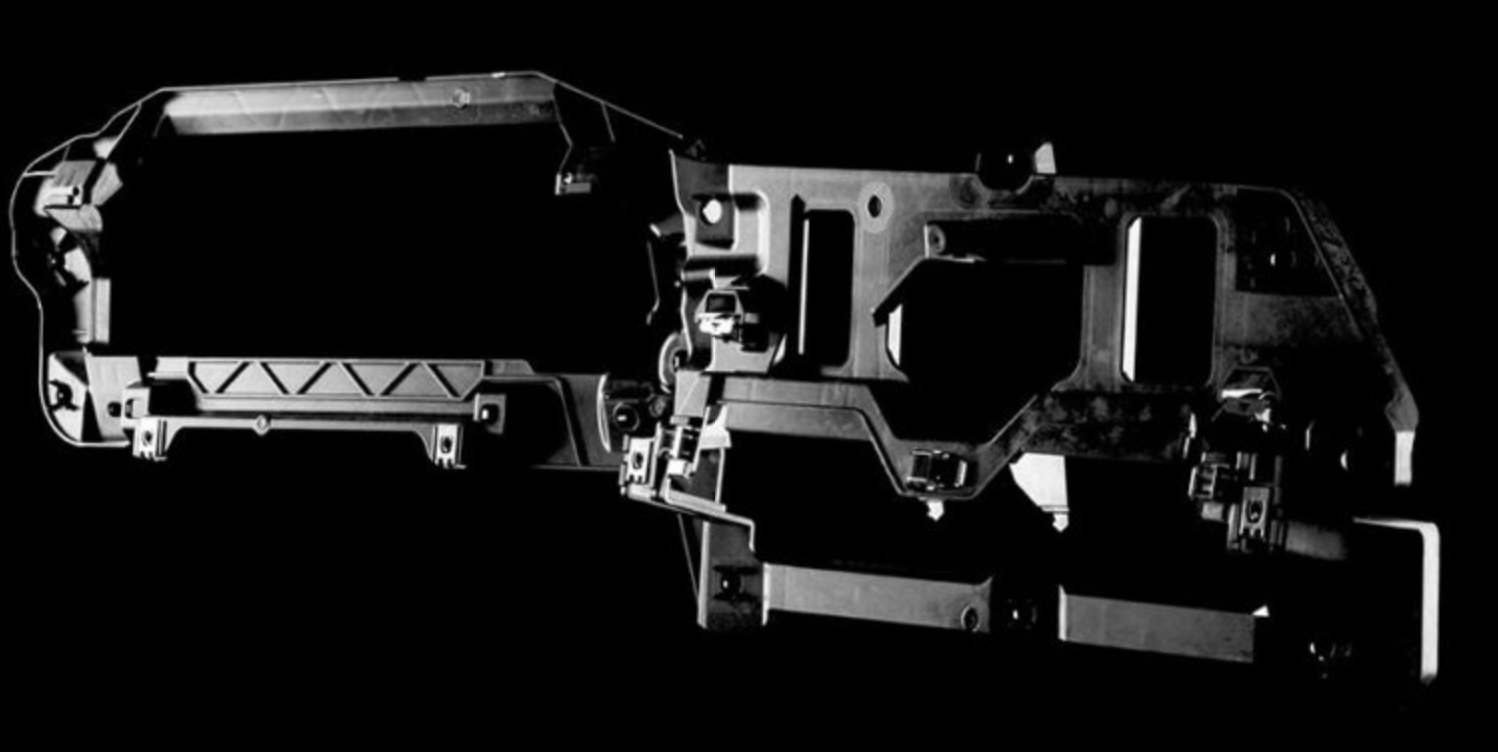
Weight Reduction – Wheels from Carbon with Decreased Wall Thickness
The trend for weight reduction continued this year. Porsche reported a significant decrease in weight by moving to production of wheels based on carbon instead of aluminum (Fig. 4). This change gave a decrease in wheel weight of approximately 2 kg per wheel while improving mechanical properties by 20%.
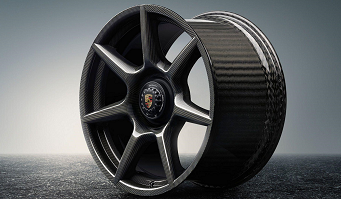
Another strategy for weight reduction is decreasing the wall thickness of parts. The standard wall thickness today for door panels is 1.6 mm. Developments are already on the way to allow reduction to 1.4 mm. This requires compounds with improved die flow together with excellent mechanical properties. Polyram supports customers interested in down-gauging starting from the engineering design stage, through the use of Moldex 3D software. Decreasing wall thickness raises an additional challenge to muffle vibrational noise. Here as well Polyram offers a total solution that includes development of suitable compounds along with engineering design services as part of customer support.
Conductive Compounds Suitable for Electrostatic Painting
One of Polyram’s ongoing projects is developing compounds for the vehicle body that allow production of plastic parts that can be painted electrostatically together with the main metal body parts. One example is plastic fuel tank doors with appearance identical to the metal body surrounding (Figure 5). To allow electrostatic painting, the plastic parts must be made from compounds giving a certain level of electrical conductivity as well as heat resistance to withstand the temperatures required for oven curing of the paint. The number of polymers meeting this last requirement is small. Polyram compounds for automotive painting applications are in advanced stages of validation.
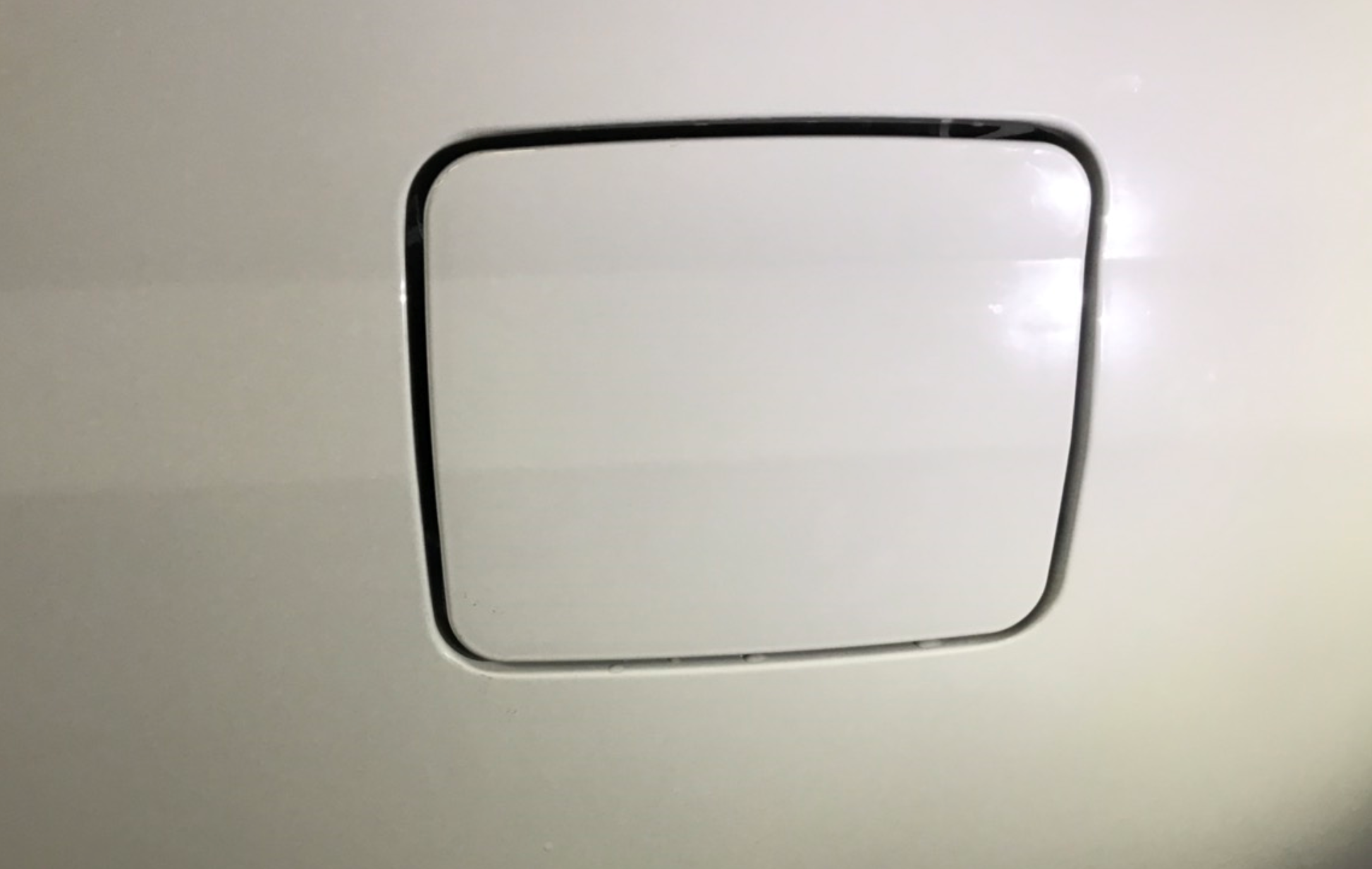